מכונת הפלטות היא מכשיר לדחיסת דלק פלטות ביומסה והזנת פלטות, שביניהם גליל הלחץ הוא המרכיב העיקרי והחלק הפגיע שלו. בשל עומס העבודה הכבד ותנאי העבודה הקשים, אפילו באיכות גבוהה, בלאי הוא בלתי נמנע. בתהליך הייצור, צריכת גלילי הלחץ גבוהה, ולכן החומר ותהליך הייצור של גלילי הלחץ חשובים במיוחד.
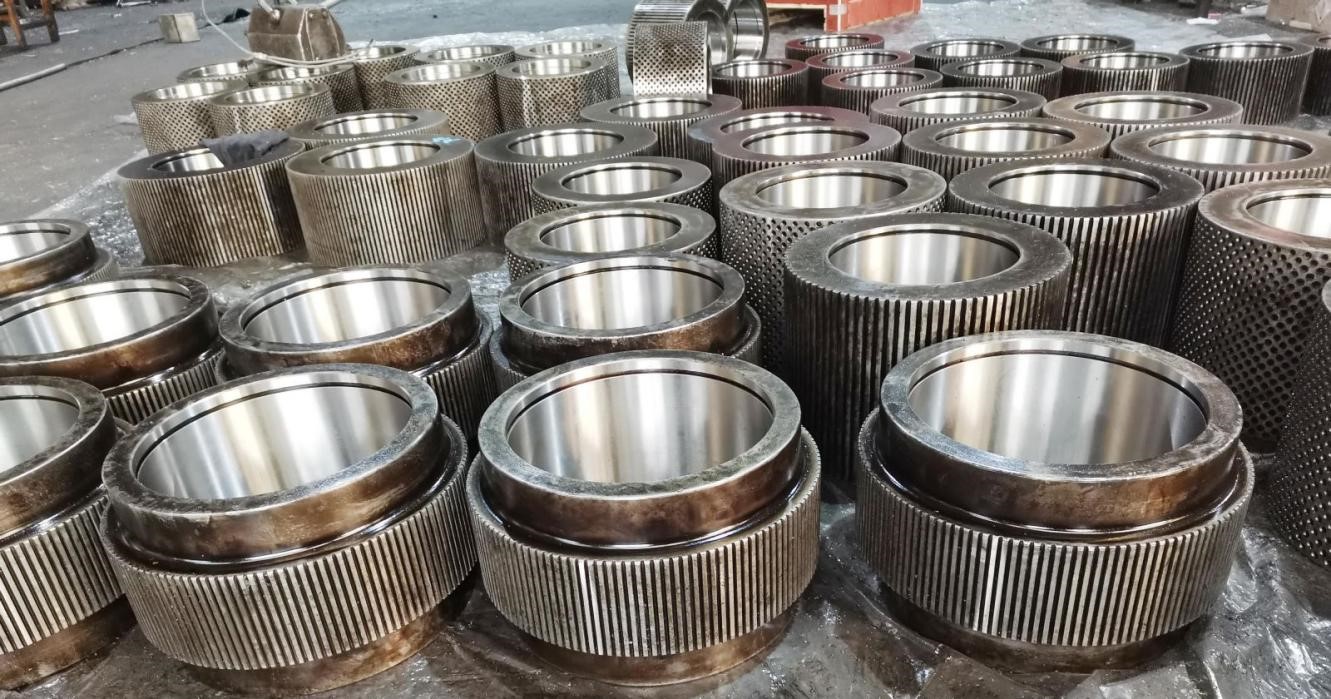
ניתוח כשל של גלגל הלחץ של מכונת החלקיקים
תהליך הייצור של גליל הלחץ כולל: חיתוך, זיוף, נרמול (חישול), עיבוד גס, מרווה והרפיה, עיבוד שבבי חצי מדויק, מרווה שטחית ועיבוד שבבי מדויק. צוות מקצועי ערך מחקר ניסיוני על בלאי של דלקי ביומסה לייצור ועיבוד, וסיפק בסיס תיאורטי לבחירה רציונלית של חומרי גליל ותהליכי טיפול בחום. להלן מסקנות המחקר והמלצותיו:
שקעים ושריטות מופיעים על פני השטח של גליל הלחץ של הגרנולטור. עקב בלאי של זיהומים קשים כמו חול וסבבי ברזל על גליל הלחץ, זה שייך לבלאי חריג. הבלאי הממוצע על פני השטח הוא כ-3 מ"מ, והבלאי משני הצדדים שונה. בצד ההזנה יש בלאי חמור, עם בלאי של 4.2 מ"מ. בעיקר בגלל העובדה שלאחר ההזנה, להומוגנייזר לא היה זמן לפזר את החומר באופן שווה ונכנס לתהליך שיחול.
ניתוח שחיקה מיקרוסקופי מראה כי עקב שחיקה צירית על פני השטח של גליל הלחץ הנגרם על ידי חומרי הגלם, חוסר בחומר פני השטח על גליל הלחץ הוא הגורם העיקרי לכשל. צורות הבלאי העיקריות הן שחיקה דביקה ובלאי שוחק, עם מורפולוגיה כגון בורות קשים, רכסי חרישה, חריצי חרישה וכו', המצביעה על כך שסיליקטים, חלקיקי חול, שבבי ברזל וכו' בחומרי הגלם גורמים לשחיקה חמורה על פני השטח של גליל הלחץ. עקב פעולת אדי מים וגורמים אחרים, מופיעות דוגמאות דמויות בוץ על פני השטח של גליל הלחץ, וכתוצאה מכך סדקי קורוזיה מאמצת על פני השטח של גליל הלחץ.
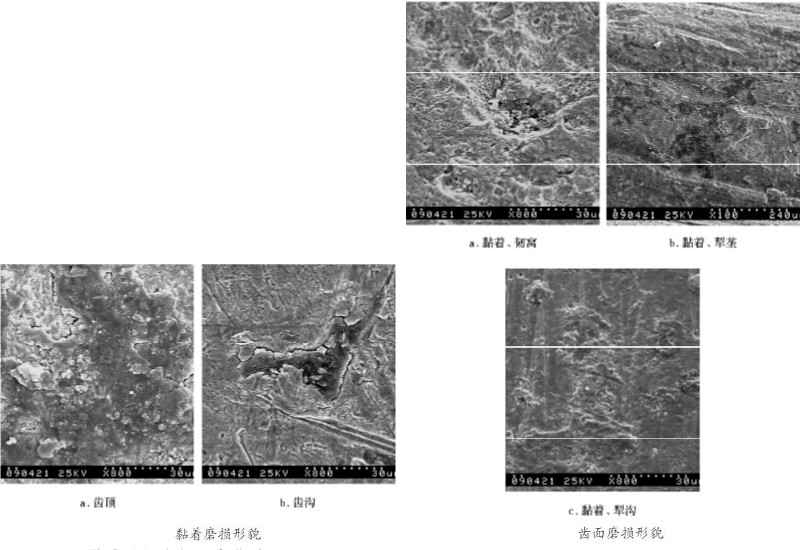
מומלץ להוסיף תהליך להסרת זיהומים לפני ריסוק חומרי הגלם כדי להסיר חלקיקי חול, שבבי ברזל וזיהומים אחרים המעורבבים בחומרי הגלם, על מנת למנוע בלאי חריג של גלילי הלחץ. יש לשנות את צורת המגרד או את מיקום ההתקנה כדי לפזר את החומר באופן שווה בתא הדחיסה, למנוע כוח לא אחיד על גליל הלחץ ולהחמיר את הבלאי על פני השטח של גליל הלחץ. בשל העובדה שגליל הלחץ נכשל בעיקר עקב שחיקה של פני השטח, על מנת לשפר את קשיות פני השטח הגבוהה שלו, עמידות הבלאי ועמידות בפני קורוזיה, יש לבחור חומרים עמידים בפני שחיקה ותהליכי טיפול בחום מתאימים.
טיפול בחומרים ובתהליך של גלילי לחץ
הרכב החומר והתהליך של גליל הלחץ הם התנאים המוקדמים לקביעת עמידות הבלאי שלו. חומרי הגליל הנפוצים כוללים C50, 20CrMnTi ו-GCr15. תהליך הייצור משתמש בכלי מכונה CNC, וניתן להתאים אישית את פני הגליל עם שיניים ישרות, שיניים אלכסוניות, סוגי קידוח וכו' בהתאם לצרכים. חימום קרבוריזציה או טיפול בחום חימום בתדירות גבוהה משמשים להפחתת עיוות הגליל. לאחר טיפול בחום, מתבצע שוב עיבוד שבבי מדויק כדי להבטיח את קונצנטריות המעגלים הפנימיים והחיצוניים, מה שיכול להאריך את חיי השירות של הגליל.
חשיבות הטיפול בחום עבור גלילי לחץ
ביצועי גליל הלחץ חייבים לעמוד בדרישות של חוזק גבוה, קשיות גבוהה (עמידות בפני שחיקה) וקשיחות גבוהה, כמו גם יכולת עיבוד טובה (כולל ליטוש טוב) ועמידות בפני קורוזיה. טיפול בחום של גלילי לחץ הוא תהליך חשוב שמטרתו לממש את הפוטנציאל של חומרים ולשפר את ביצועיהם. יש לו השפעה ישירה על דיוק הייצור, חוזק, אורך חיים ועלויות הייצור.
עבור אותו חומר, חומרים שעברו טיפול התחממות יתר הם בעלי חוזק, קשיות ועמידות גבוהים בהרבה בהשוואה לחומרים שלא עברו טיפול התחממות יתר. אם לא יבוצע תהליך קירור, חיי השירות של גליל הלחץ יהיו קצרים בהרבה.
אם רוצים להבחין בין חלקים שעברו טיפול בחום לחלקים שלא עברו טיפול בחום שעברו עיבוד מדויק, אי אפשר להבחין ביניהם אך ורק לפי קשיות וצבע חמצון בטיפול בחום. אם לא רוצים לחתוך ולבדוק, אפשר לנסות להבחין ביניהם באמצעות צליל נקישה. המבנה המטלוגרפי והחיכוך הפנימי של יציקות וחלקי עבודה שעברו תהליך של קירור ומחוסם שונים, וניתן להבחין ביניהם באמצעות נקישה עדינה.
קשיות הטיפול בחום נקבעת על ידי מספר גורמים, כולל סוג החומר, גודלו, משקלו, צורתו ומבנהו, ושיטות העיבוד הבאות. לדוגמה, בעת שימוש בחוט קפיצי לייצור חלקים גדולים, עקב העובי בפועל של חומר העבודה, המדריך מציין כי קשיות הטיפול בחום יכולה להגיע ל-58-60HRC, דבר שלא ניתן להשיג בשילוב עם חומר עבודה בפועל. בנוסף, מדדי קשיות לא סבירים, כגון קשיות גבוהה מדי, עלולים לגרום לאובדן קשיחות חומר העבודה ולגרום לסדקים במהלך השימוש.
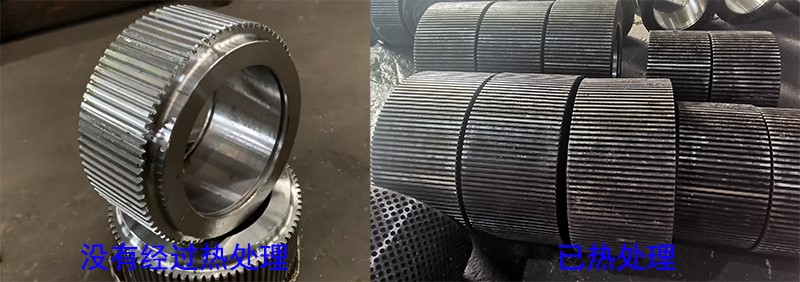
טיפול בחום צריך לא רק להבטיח ערך קשיות מוסמך, אלא גם לשים לב לבחירת התהליך ולבקרת התהליך. חימום יתר של חימום וריסוס יכולים להשיג את הקשיות הנדרשת; באופן דומה, תחת חימום במהלך הריסוס, התאמת טמפרטורת הריסוס יכולה גם היא לעמוד בטווח הקשיות הנדרש.
גליל הלחץ של Baoke עשוי מפלדת C50 איכותית, מה שמבטיח את הקשיות והעמידות בפני שחיקה של גליל הלחץ של מכונת החלקיקים מהמקור. בשילוב עם טכנולוגיית טיפול בחום מעולה בטמפרטורה גבוהה, הוא מאריך מאוד את חיי השירות שלו.
זמן פרסום: 17 ביוני 2024