עמידות נמוכה למים, משטח לא אחיד, תכולת אבקה גבוהה ואורך לא אחיד? בעיות נפוצות ואמצעי שיפור בייצור מזון ימי
בייצור היומיומי שלנו של מזון ימי, נתקלנו בכמה בעיות ממגוון היבטים. הנה כמה דוגמאות שכדאי לדון בהן עם כולם, כדלקמן:
1. נוּסחָה
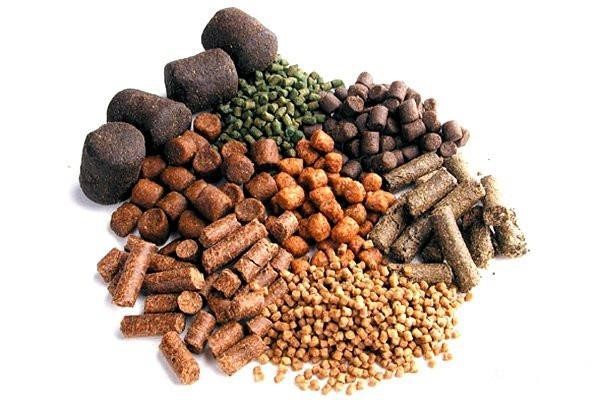
1. במבנה הנוסחה של מזון לדגים, ישנם סוגים רבים יותר של חומרי גלם לקמח, כגון קמח קנולה, קמח כותנה וכו', השייכים לסיבים גולמיים. בחלק ממפעלי הנפט יש טכנולוגיה מתקדמת, והשמן מטוגן בעיקרון יבש עם תכולה נמוכה מאוד. יתר על כן, חומרי גלם מסוג זה אינם נספגים בקלות בייצור, דבר המשפיע רבות על הגרנולציה. בנוסף, קמח כותנה קשה לכתישה, דבר המשפיע על היעילות.
2. פתרון: השימוש בעוגת קנולה הוגבר, ונוספו לפורמולה מרכיבים מקומיים איכותיים כמו סובין אורז. בנוסף, נוספה חיטה, המהווה כ-5-8% מהפורמולה. באמצעות התאמות, אפקט הגרנולציה בשנת 2009 היה אידיאלי יחסית, וגם התשואה לטון גדלה. חלקיקי 2.5 מ"מ נעים בין 8-9 טון, עלייה של כמעט 2 טון בהשוואה לעבר. גם מראה החלקיקים השתפר משמעותית.
בנוסף, כדי לשפר את יעילות ריסוק קמח זרעי הכותנה, ערבבנו קמח זרעי כותנה וקמח קנולה ביחס של 2:1 לפני הריסוק. לאחר השיפור, מהירות הריסוק הייתה כמעט זהה למהירות הריסוק של קמח קנולה.
2, משטח לא אחיד של חלקיקים
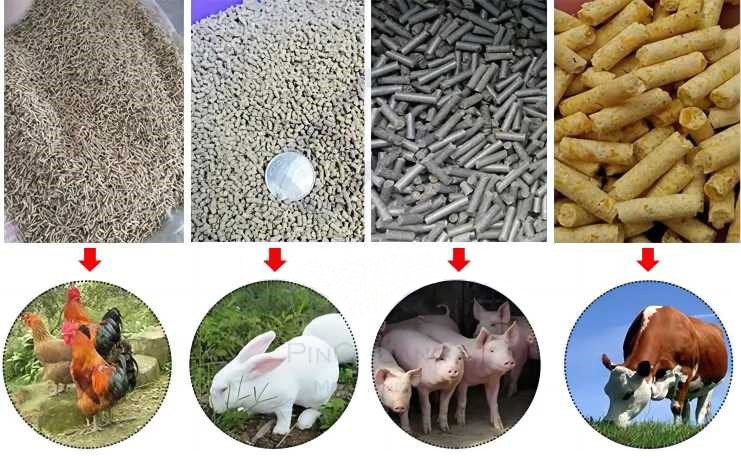
1. יש לו השפעה רבה על מראה המוצר המוגמר, וכאשר מוסיפים אותו למים, הוא נוטה לקרוס ושיעור ניצול נמוך. הסיבה העיקרית היא:
(1) חומרי הגלם נמעכים גס מדי, ובמהלך תהליך ההרפיה הם אינם מתבשלים ומתרככים במלואם, ולא ניתן לשלב אותם היטב עם חומרי גלם אחרים בעת מעברם דרך חורי התבנית.
(2) בנוסחת מזון לדגים עם תכולה גבוהה של סיבים גולמיים, בשל נוכחות בועות קיטור בחומר הגלם במהלך תהליך ההרפיה, בועות אלו נקרעות עקב הפרש הלחצים בין פנים התבנית לחוץ שלה במהלך דחיסת החלקיקים, וכתוצאה מכך משטח החלקיקים אינו אחיד.
2. אמצעי טיפול:
(1) לשלוט בתהליך הריסוק כראוי
כיום, בעת ייצור מזון לדגים, חברתנו משתמשת באבקת מיקרו-מסננת בעובי 1.2 מ"מ כחומר גלם בכמות גדולה. אנו שולטים בתדירות השימוש במסננת ובמידת הבלאי של הפטיש כדי להבטיח את מידת הדק של הריסוק.
(2) בקרת לחץ קיטור
בהתאם לנוסחה, יש להתאים את לחץ הקיטור באופן סביר במהלך הייצור, בדרך כלל בשליטה סביב 0.2. בשל הכמות הגדולה של חומרי גלם מסיבים גסים בנוסחת מזון לדגים, נדרש קיטור איכותי וזמן הרפיה סביר.
3. עמידות נמוכה למים של חלקיקים
1. בעיה מסוג זה היא הנפוצה ביותר בייצור היומיומי שלנו, והיא קשורה בדרך כלל לגורמים הבאים:
(1) זמן הרפיה קצר וטמפרטורת הרפיה נמוכה גורמים להרפיה לא אחידה או לא מספקת, דרגת הבשלה נמוכה ולחות לא מספקת.
(2) חומרי דבק לא מספיקים כגון עמילן.
(3) יחס הדחיסה של תבנית הטבעת נמוך מדי.
(4) תכולת השמן ושיעור חומרי הגלם הסיבים הגולמיים בנוסחה גבוהים מדי.
(5) גורם גודל החלקיקים לריסוק.
2. אמצעי טיפול:
(1) לשפר את איכות הקיטור, להתאים את זווית הלהב של הרגולטור, להאריך את זמן ההרפיה, ולהגדיל כראוי את תכולת הלחות של חומרי הגלם.
(2) התאימו את הנוסחה, הגדילו בהתאם את חומרי הגלם של העמילן והפחיתו את שיעור חומרי הגלם של השומן והסיבים הגולמיים.
(3) הוסיפו דבק במידת הצורך. (תערובת בנטוניט על בסיס נתרן)
(4) שיפור יחס הדחיסה שלטבעת למות
(5) שלטו היטב בדקילות הריסוק
4, תכולת אבקה מוגזמת בחלקיקים
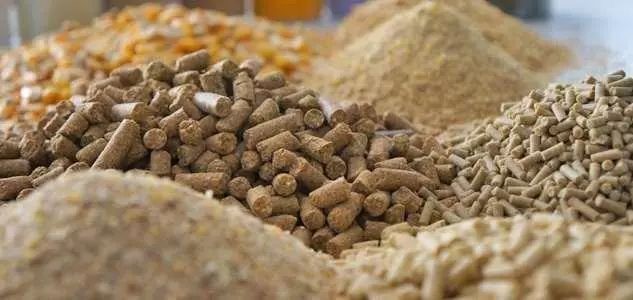
1. קשה להבטיח את מראה הזנת הכדורים הכללית לאחר קירור ולפני סינון. לקוחות דיווחו שיש יותר אפר דק ואבקה בכדורים. בהתבסס על הניתוח לעיל, אני חושב שישנן מספר סיבות לכך:
א. פני השטח של החלקיקים אינם חלקים, החתך אינו מסודר, והחלקיקים רופפים ונוטים להיווצרות אבקה;
ב. סינון לא שלם על ידי מסך דירוג, רשת מסך סתומה, בלאי חמור של כדורי גומי, פתח רשת מסך לא תואם וכו';
ג. יש הרבה שאריות אפר דק במחסן המוצר המוגמר, והפינוי אינו יסודי;
ד. קיימות סכנות נסתרות בהסרת אבק במהלך האריזה והשקילה;
אמצעי טיפול:
א. אופטימיזציה של מבנה הנוסחה, בחירת תבנית הטבעת בצורה סבירה, ושליטה טובה ביחס הדחיסה.
ב. במהלך תהליך הגרנולציה, יש לשלוט על זמן ההרפיה, כמות ההזנה וטמפרטורת הגרנולציה כדי להבשיל ולרכך את חומרי הגלם במלואם.
ג. ודאו שחתך הרוחב של החלקיקים מסודר והשתמשו בסכין חיתוך רכה העשויה מפלדת פס.
ד. התאם ותחזק את מסך הדירוג, והשתמש בתצורת מסך סבירה.
ה. השימוש בטכנולוגיית סינון משנית מתחת למחסן המוצר המוגמר יכול להפחית במידה ניכרת את יחס תכולת האבקה.
ו. יש צורך לנקות את מחסן המוצר המוגמר ואת המעגל בצורה יעילה. בנוסף, יש צורך לשפר את האריזה ומכשיר הסרת האבק. עדיף להשתמש בלחץ שלילי להסרת אבק, וזה אידיאלי יותר. במיוחד במהלך תהליך האריזה, עובד האריזה צריך לדפוק ולנקות באופן קבוע את האבק ממיכל הבופר של משקל האריזה..
5, אורך החלקיקים משתנה
1. בייצור היומיומי, אנו נתקלים לעתים קרובות בקשיי בקרה, במיוחד עבור דגמים מעל 420. הסיבות לכך מסוכמות באופן גס כדלקמן:
(1) כמות ההאכלה לגרנולציה אינה אחידה, ואפקט ההרפיה משתנה מאוד.
(2) פער לא עקבי בין גלילי התבנית או בלאי חמור של תבנית הטבעת וגלילי הלחץ.
(3) לאורך כיוון הציר של תבנית הטבעת, מהירות הפריקה בשני הקצוות נמוכה יותר מזו שבאמצע.
(4) חור הפחתת הלחץ של תבנית הטבעת גדול מדי, וקצב הפתיחה גבוה מדי.
(5) מיקום וזווית להב החיתוך אינם סבירים.
(6) טמפרטורת גרנולציה.
(7) לסוג ולגובה האפקטיבי (רוחב הלהב, רוחב) של להב חיתוך הטבעת יש השפעה.
(8) במקביל, פיזור חומרי הגלם בתוך תא הדחיסה אינו אחיד.
2. איכות המזון והכדורים מנתחת בדרך כלל על סמך התכונות הפנימיות והחיצוניות שלהם. כמערכת ייצור, אנו חשופים יותר לדברים הקשורים לאיכות החיצונית של כדורי מזון. מנקודת מבט של ייצור, ניתן לסכם באופן גס את הגורמים המשפיעים על איכות כדורי המזון המימיים כדלקמן:
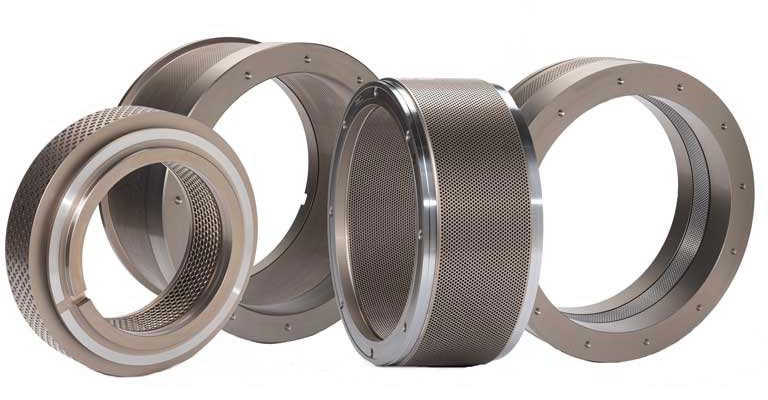
(1) לתכנון ולארגון של נוסחאות יש השפעה ישירה על איכות כדורי המזון המימיים, והם מהווים כ-40% מהסך הכל;
(2) עוצמת הריסוק ואחידות גודל החלקיקים;
(3) הקוטר, יחס הדחיסה והמהירות הליניארית של תבנית הטבעת משפיעים על אורך וקוטר החלקיקים;
(4) יחס הדחיסה, המהירות הליניארית, אפקט הקיבוע והחיסום של תבנית הטבעת, והשפעת להב החיתוך על אורך החלקיקים;
(5) תכולת הלחות של חומרי הגלם, אפקט הרפיה, קירור וייבוש משפיעים על תכולת הלחות והמראה של מוצרים מוגמרים;
(6) הציוד עצמו, גורמי התהליך והשפעות החימום והכיבוי משפיעים על תכולת אבקת החלקיקים;
3. אמצעי טיפול:
(1) יש להתאים את האורך, הרוחב והזווית של מגרד הבד, ולהחליף את המגרד השחוק.
(2) יש לשים לב להתאמת מיקום להב החיתוך בצורה יעילה בתחילת ובסוף הייצור עקב כמות ההזנה הקטנה.
(3) במהלך תהליך הייצור, יש לוודא קצב הזנה ואספקת קיטור יציבים. אם לחץ הקיטור נמוך והטמפרטורה אינה יכולה לעלות, יש לכוונן או להפסיקו בזמן.
(4) להתאים באופן סביר את הפער ביןמעטפת רולרהתקינו גלילים חדשים לאחר התבנית החדשה, ותקנו מיד את המשטח הלא אחיד של גליל הלחץ ותבנית הטבעת עקב בלאי.
(5) תקן את חור ההנחיה של תבנית הטבעת ונקה מיד את חור התבנית הסתום.
(6) בעת הזמנת תבנית הטבעת, יחס הדחיסה של שלוש שורות החורים בשני קצוות כיוון הציר של תבנית הטבעת המקורית יכול להיות קטן ב-1-2 מ"מ מזה שבאמצע.
(7) השתמשו בסכין חיתוך רכה, בעובי מבוקר בין 0.5-1 מ"מ, כדי להבטיח קצה חד ככל האפשר, כך שהוא יהיה על קו הרשת בין תבנית הטבעת לגלגל הלחץ.
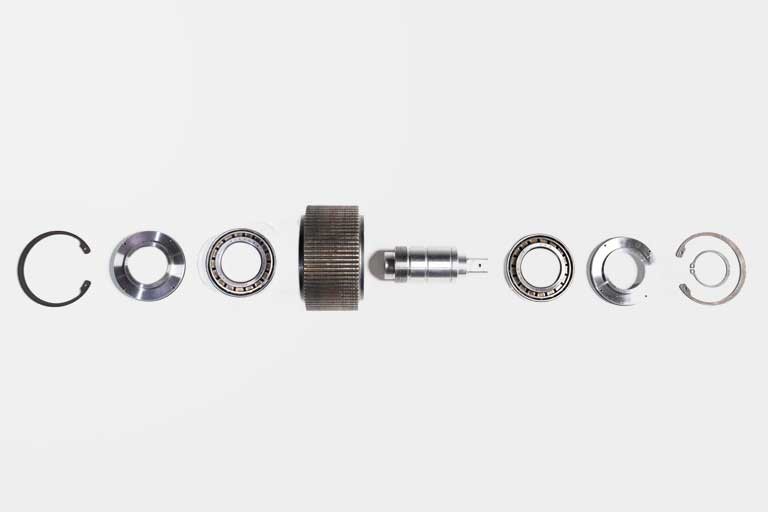
(8) יש לוודא את הקונצנטריות של תבנית הטבעת, לבדוק באופן קבוע את מרווח הציר של הגרנולטור, ולהתאים אותו במידת הצורך.
6, סיכום נקודות בקרה:
1. טחינה: יש לשלוט על מידת הדקיקות של הטחינה בהתאם לדרישות המפרט.
2. ערבוב: יש לשלוט באחידות ערבוב חומרי הגלם על מנת להבטיח כמות ערבוב, זמן ערבוב, תכולת לחות וטמפרטורה מתאימים.
3. התבגרות: יש לשלוט בלחץ, בטמפרטורה ובלחות של מכונת ההתפחה
גודל וצורת חומר החלקיקים: יש לבחור מפרטים מתאימים של תבניות דחיסה ולהבי חיתוך.
5. תכולת המים של המזון המוגמר: יש לוודא את זמן הייבוש והקירור והטמפרטורה.
6. ריסוס שמן: יש צורך לשלוט בכמות הריסוס המדויקת, במספר הפיה ובאיכות השמן.
7. סינון: בחר את גודל הנפה בהתאם למפרט החומר.
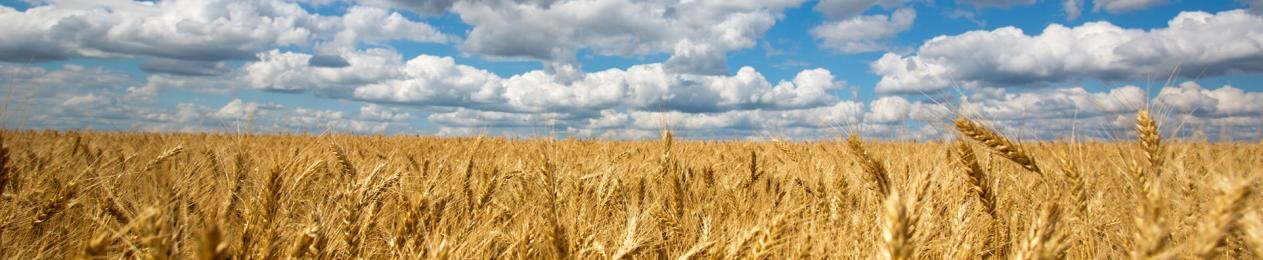
זמן פרסום: 30 בנובמבר 2023